Designing a simpler and lower cost solar tracking amplifier
|
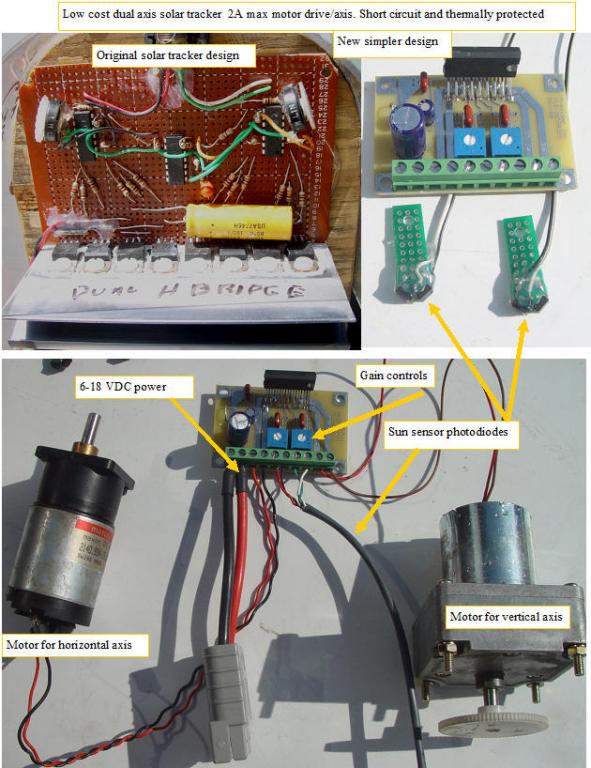 | |
New low cost dual solar tracker
|
I have been using a dual H bridge solar tracker design for many years, but it has a lot of parts, is relatively cheap, but takes some time to build on a breadboard. I needed to make another tracker for a new small solar dish, and decided to take a new look at the circuit. After some research I found a nice solution. Since a single power supply is how I wanted to power the system, a full bridge servo amplifier which can source or sink current through the motor in either direction was a requirement. I found that a bridge tied load audio amplifier chip if dc connected rather than the ac coupling that it was designed for will do the job nicely.I built a prototype on a breadboard, and found that it worked as well as the much more complex and expensive discrete component version that I have been building, and only has a few support components, so it is both inexpensive and easy to build. a schematic of the circuit: IC dual solar tracker After some further tweaking of the design, I will be offering the built and ready to use dual tracker system including the photo diode solar sensors as a product. Buddy Paul Provost laid out the pc board so that the circuit could also be used as the 15W stereo amplifier that it was designed for by simply cutting two etches and adding some capacitors. The circuit can also be used as a dual position feedback servo by using a feedback potentiometer geared to the motor output on the +input and a position command potentiometer on the - input. The motor will turn and rotate the feedback potentiometer to the position commanded by the command potentiometer. The command can also be generated by a computer with a PWM or analog output. The board is designed with the chip on one edge, so the chip can be attached to a heatsink or chassis. My first test with 1-2A draw showed minimal heating of the chip, so only a minimal heatsink is required unless the system is pushed to the 2A limit frequently. As with any tracking system, mechanical design can make or break the system. The axis should have balanced loads so the servo does not need to continuously drive current into an axis just to hold position.
|
|