Welding beautifully
|
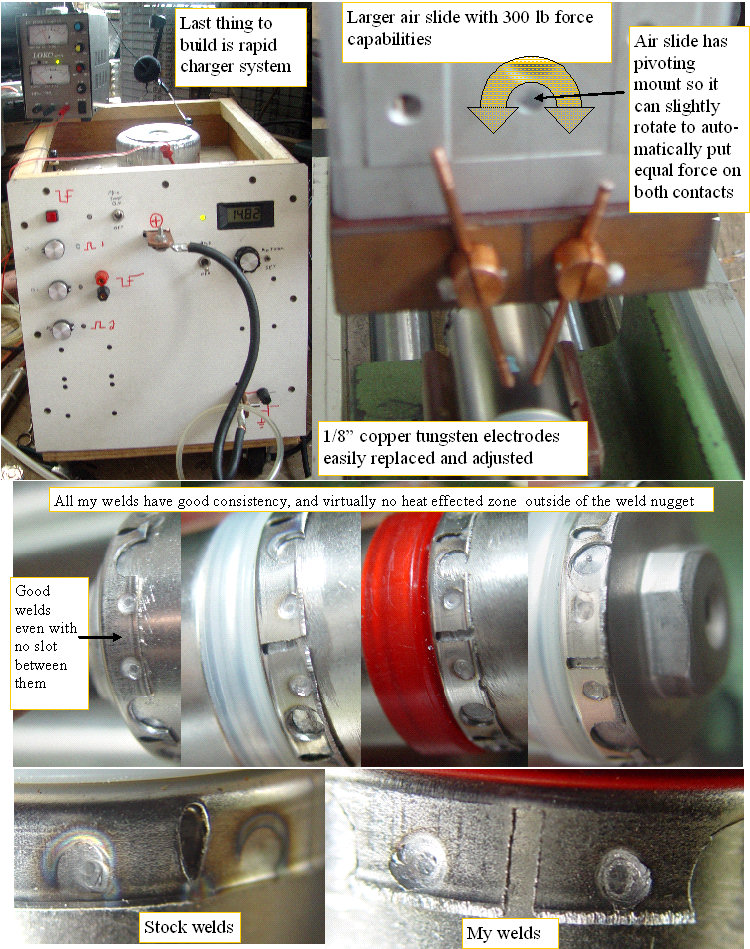 | |
New Weld fixture looking good
|
Finally got back to my spotwelder. For production welding I determined that my weld head had to have certain features. 1. easy to align 2. easy to build 3. automatically adjust to uneven surfaces 4. be able to press the contacts into the cells with up to 300 lbs of force 5. easy to replace the weld tips with minimal time required for changeover and adjustment.
The new design uses a much bigger air powered slide that can provide over 300 lb of force @ 100psi inlet pressure. The slide is mounted to a bridge assembly so the mount will not deflect when pushing. The welding rods are clamped by a set screw, and can slide in or out easily. The rods pass through a hole in a 1/2" copper bar that is tapped on the rear side so the large ring terminals of the weld cables can simply be bolted on with some 1/4-20 bolts. The cell supports were changed to full V blocks to better support the cells under the high contact force. The 1/2 " rods pass through a block of linen phenolic and are held in position by two set screws. Very easy to make, and it allows a lot of adjustment flexibility. The welds look good, and I only had one blow out, when I turned the second weld pulse way up. I can dump >90% of the 15V 4.7 Farad capacitors charge into the weld if required, but it only takes bit over half to make good welds. I even can weld without the slot between the contacts. The best part is that it makes welds over a wide range of timing variations. The only thing I don't like about the design is that the first short conditioning pulse is using the max cap voltage, and the second one only has whats left for voltage to work with. Once I can charge the cap at 50A instead of 3A, that difference should be negligible and will be controlled by the delay for charging before the second pulse. In all, I think I have a dual pulse CD welder that is nearly ready for production use.
|
|