How do the big guys do it
|
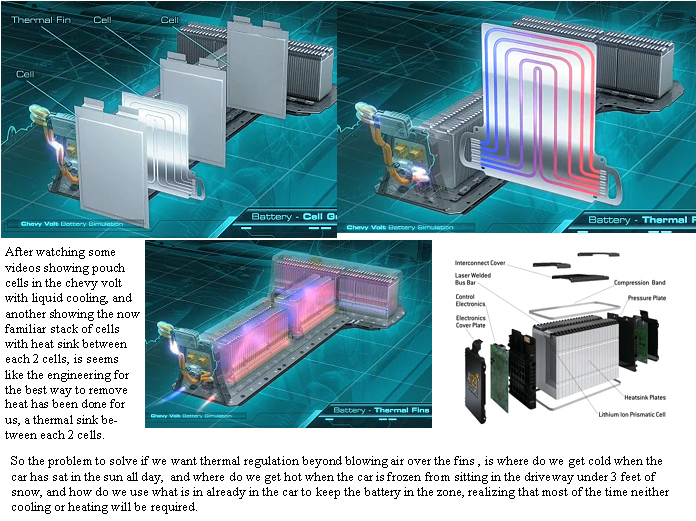 | |
How do the big guys do it?
|
After the initial experiments,and getting a better feel for the characteristics of these cells, I did some searching for how these type cells are cooled in real world applications. Both of the pictured automotive systems have liquid cooling of the pack. A commercial vehicle that can be sold in the 50 states needs to operate over some big extremes in environment. The guys that have seen their Insight or Civic start on the 12V starter in winter ,can also be the ones that could get the inside of the car to 120F in a parking lot in summer, so to design a pack, one needs to decide if they are willing to risk battery damage at the extremes, or do we want to provide active cooling heating into the system. So lets throw out some ideas: The AC can generate cold, and the heater can generate hot, so an air fluid heat exchanger right in the AC/heater ducting with separate insulated fluid handling system to a heat exchanger along the sides of the pack as in the bottom photo, or possibly a ducted path for the heater / AC output to the pack blowing over the extended fins of the thermal spacers. The two cells/ heat exchanger plate probably works fine when you can send chilled fluid through a heatsink on the plates or through the plate it self like the volt.
For an air cooled system, a plate between each cell would provide the best solution. The problem comes when you have a car at 120F and everything in it including the air and battery is at the same temperature. The opposite when the car and batteries are frozen at 10 below zero. In a garage, AC power could keep the pack in the zone, but then you are in trouble if the car is not home and you need to overnight in cold climates. The cells are rated to operate to -22, but based on the changes I see at 40F, I would not expect much performance in below zero temperatures, and to wait for the car to warm up and then the warm air to heat the pack, and you may be at your destination before your in the best temperature zone?
|
|