PLUG in adapters for fan and current sensor
|
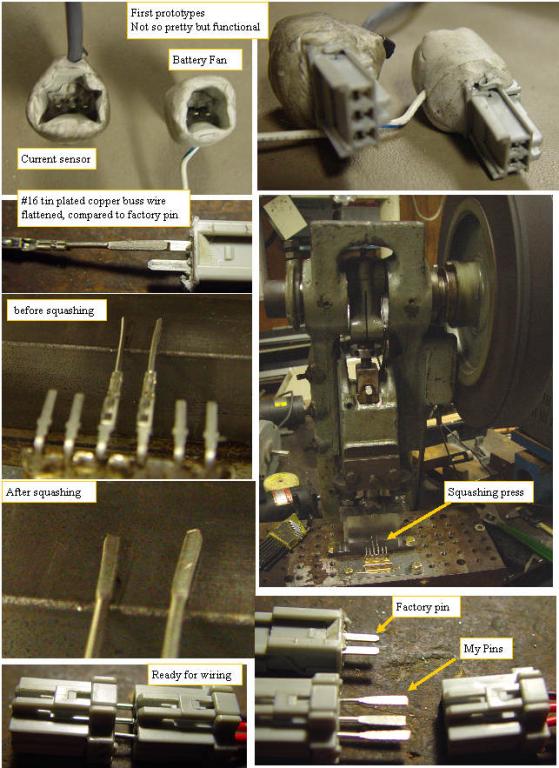 | |
Forming the male pins
|
After striking out on identifying a source for the socket side of the fan and current sensor connectors, I needed to figure out how to make 500 male female pins for the 3 pin and 2 pin connectors. I want the adapters to securely support the harness connector that will plug into the adapter, be low profile, and be strong and reliable connections so the stock signals are not effected. The honda connectors pins are almost exactly the same width and thickness as the larger of the Amp Tyco connectors, but it is not cost effective to pull the 13 pins out of the $12 104 pin headers, so I did some experimenting and found that #16 tin plated copper buss wire if squashed to the .024" thickness that the stock pins are, gets to nearly the same width as the stock pins, and the squashing seems to leave the tin plating intact. I used the display cover punch fixture with a pin holder made from a cabinet hinge, to hold the pins in the correct position for squashing. The resultant pin is strong, and easy to attach wires to, and I can get 350 of them out of 1/4 lb roll of the wire. Next task, the connector shell.
|
|