|
|
Some ideas for a better world | 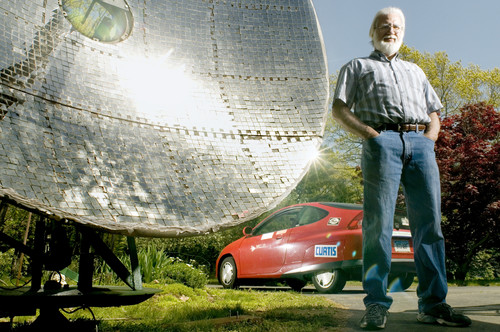 | | Mike and his toys |
Mikes car modifications can be found here: Mikes Insight For information on the original MIMA systems please check here: MIMA
Is your hybrid car battery having HV Battery problems, Check out the GCO1 Hybrid Car battery charger. This High Voltage constant current battery charger/conditioner can recondition your battery pack. Over 80% of packs responding with no more fault codes, and increased performance: CHARGER The charger design was sold to Hybrid Revolt, so any inquiries about chargers or accessories should be directed there Hybrid Revolt Charger
The world economy is a mess, green house warming is melting the glaciers and poles, the breadbaskets of the world are suffering drying conditions, people are losing their jobs and retirement funds. It can be a bit depressing to look at the current and future prospects, but the boy scouts motto of "Be Prepared" is good advice for us all, and if we act wisely and quickly, and in mass, the slope of decline can be extended so we have more time to make the required changes to get to a sustainable world.
Why the urgency? Don't we have solar, wind, hydrogen , Ethanol , electric cars. The enormous cost of bringing these technologies into widespread use, depends on a healthy economy with the resources to make it happen. Not exactly where we are right now. I can only hope that our leaders are making the right moves at this critical time.
In my opinion, The best way towards sustainability is for each of us to give a lot of thought and action towards changing our lifestyle to a much more efficient one,and not depend on some magic new technology. Many inexpensive ways to save energy are all over the web, get your families involved, and share the techniques with anyone interested while encouraging them to change as well. Hopefully some of what I share on this website will make a difference for some of you. One Hundred years from now, we will be either an extinct species in a recovering world, or will be living in a society that has learned to live in a sustainable way with nature.
A big change in each of our energy footprints could almost overnight make a huge change in how long we have to solve the massive problems we, and our children are facing. Now that I have passed the MIMA and gridcharger projects to others, I am devoting all of my time to getting my shop and home projects finished, and will soon begin to blog about what is happening.
If you would like to get involved or support any of these projects, please contact me at (860)935-5569 My Background:
Together we can make a huge difference. Sincerely Mike Dabrowski, Manager Genesis One, LLC
|
|
|
|
|